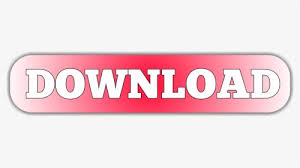

Compressors are designed with adequate margin to ensure that this area of instability ( Figure 4–33) is avoided. In this case there is an instantaneous breakdown of flow through the machine and the high-pressure air in the combustion system is expelled forward through the compressor with a loud “bang” and a resultant loss of engine thrust. If the engine demands a pressure rise from the compressor that is higher than the blading can sustain, “surge” occurs. The former is a front stage problem at low speeds and the latter usually affects the rear stages at high speed either can lead to blade vibration that can induce rapid destruction. These phenomena may take one of two forms: the blades may stall because the angle of incidence of the air relative to the blade is too high (positive incidence stall) or too low (negative incidence stall). If the operating conditions imposed upon the compressor blade depart too far from the design intention, breakdown of airflow and/or aerodynamically induced vibration will occur.

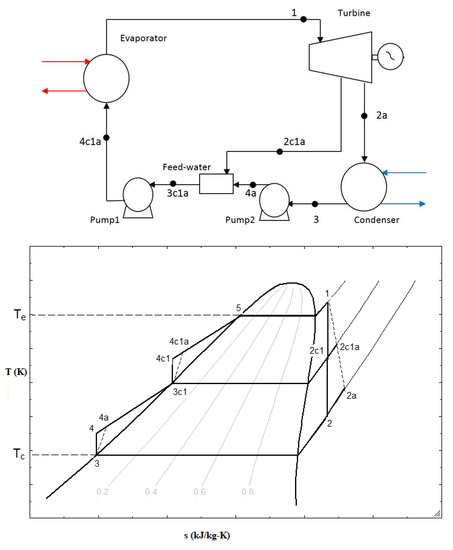
(Source: Stephen Hall, Rules of Thumb for Chemical Engineers, 5 th ed. Flow control with suction throttling valve, inlet guide vanes, discharge diffusion vanes, or speed variation.Īdvantages: High efficiency over a wide operating range, oil and pulsation free, flow and power consumption can be reduced up to 50% without using a recycle or blow-off line.ĭisadvantages: Lower capacity machines more expensive than PD alternatives. Variable flow machines commonly used to move air or gas up to a 3:1 compression ratio for either pressure or vacuum duty. PD blower with external timing gears to precisely control the position of the rotors. Vertically split machines are modular, with ability to change the number of compression stages to meet operating requirements.Īdvantages: gas flow can be controlled with a suction throttling valve at constant speed, inlet guide vanes, or speed variation. Horizontally split machines provide access to rotors, diaphragms, and bearings without disturbing piping. Non-contacting impellers operate dry, producing oil-free air or gas.Īdvantages: minor variations in flow compared to differential pressure, reliable, competitive cost.ĭisadvantages: noisy, small internal clearances are unforgiving if solids or dusts are present.ġ4 to 310 kPa (2 to 45 psig) 85 to > 170,000 m 3/h (50 to > 100,000 cfm). PD blower, used for pressure and vacuum service, up to 2:1 compression ratio.

Single stage 14 to 100 kPa (2 to 15 psig) multistage to 275 kPa (40 psig) with interstage cooling to 85,000 m 3/h (50,000 cfm) vacuum to 50 kPa (15 inches Hg).
Two stage compressor system pro ii simulation free#
Discharged gas is usually the same temperature as the incoming sealing liquid, and is saturated with the liquid.Īdvantages: excellent for use in severe operating conditions extremely simple and low maintenance delivered air is cool and free of dust or oil quiet.ĭisadvantages: higher power consumption, large quantity of cooling water needed, cost of exotic materials to withstand corrosion from sealing liquid (in some cases). Rotary positive displacement blower, used for pressure and vacuum service, sealed with a low viscosity liquid (usually water, but can be any liquid that is compatible with the blower and process). Rotary centrifugal blower with non-contacting impeller, providing oil-free air or gas.Īdvantages: compact, relatively quiet, cost competitive.ĭisadvantages: pressure limitation, fluctuations in flow and efficiency with pressure changes when compared with PD blowers.Ġ to 250 kPa (0 to 35 psig) duty, 12 to 20,000 m 3/h (7 to 12,000 cfm).
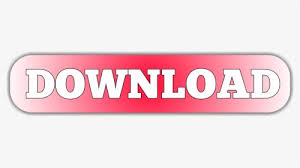